Precision in Motion Unleashing the Potential of Hysteresis Brakes Dynamometers and Advanced Motor Testing Systems
In the realm of industrial innovation, the ability to control, measure, and optimize mechanical systems is paramount. Whether it’s for automotive development, aerospace engineering, or industrial automation, the tools that enable precise torque management, dynamic testing, and energy-efficient operation are the unsung heroes of modern manufacturing. Among these tools, hysteresis brakes, hysteresis dynamometers, hysteresis clutches, and integrated motor test systems stand out as critical components that drive efficiency, reliability, and performance.
This article explores the transformative role of these technologies, highlighting their unique capabilities, applications, and the value they bring to industries worldwide.
UNDERSTANDING HYSTERESIS TECHNOLOGY: THE SCIENCE BEHIND THE MAGIC
At the heart of hysteresis devices lies a principle rooted in electromagnetic phenomena. Unlike conventional friction-based systems, hysteresis technology leverages the magnetic properties of materials to generate torque or resistance without physical contact. Appliance motor lifespan evaluation -contact operation eliminates wear and tear, ensuring longevity and consistent performance even under demanding conditions.
Hysteresis Brakes: The Silent Guardians of Precision
Hysteresis brakes are engineered to provide smooth, controllable braking torque across a wide speed range. Their design eliminates the need for mechanical friction, making them ideal for applications requiring quiet operation and minimal maintenance.
Key Advantages:
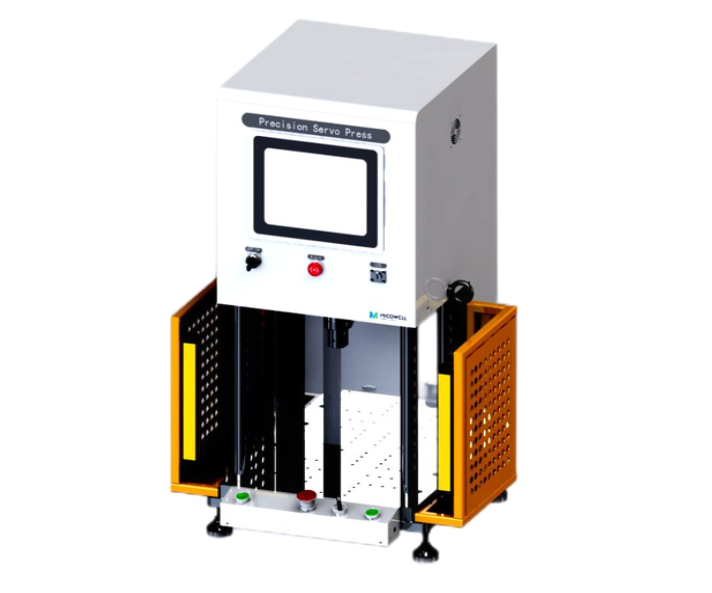
- Zero Wear: With no physical contact between components, hysteresis brakes avoid the degradation seen in traditional friction brakes.
- Linear Torque Control: Torque output is proportional to the input current, enabling precise adjustments for applications like tension control in winding machines or precision positioning in robotics.
- High-Speed Compatibility: Capable of operating at speeds exceeding 20,000 RPM, these brakes excel in high-performance environments such as turbine testing or electric motor validation.
Applications in Industry:
- Packaging Machinery: Ensuring consistent tension in film or foil winding processes.
- Medical Devices: Providing controlled resistance in surgical robots or diagnostic equipment.
- https://output.jsbin.com/socomevonu/ : Testing wind turbine generators under variable load conditions.
Hysteresis Dynamometers: The Gold Standard for Power Measurement
When it comes to measuring the performance of motors, engines, or transmissions, hysteresis dynamometers offer unparalleled accuracy. These devices absorb and measure mechanical power by converting it into heat through electromagnetic resistance, all while maintaining precise control over load conditions.
Why Choose Hysteresis Dynamometers?
- Broad Speed and Torque Range: Capable of handling everything from low-speed industrial motors to high-RPM automotive engines.
- Dynamic Response: Rapid adjustments to load changes make them ideal for simulating real-world operating conditions during R\u0026D.
- Energy Efficiency: Unlike hydraulic or eddy current systems, hysteresis dynamometers require no external cooling, reducing operational costs.
Real-World Use Cases:
- Automotive Testing: Evaluating electric vehicle motors for efficiency and thermal performance.
- Packaging machinery control : Validating the durability of aircraft actuators under extreme loads.
- Consumer Electronics: Testing the torque consistency of small motors in appliances or drones.
Hysteresis Clutches: Bridging Precision and Power
Hysteresis clutches combine the benefits of non-contact operation with the ability to transmit torque smoothly. These devices are particularly valuable in applications requiring slip control or overload protection without mechanical wear.
Standout Features:
- Slip Control: Maintains constant torque regardless of speed differentials, perfect for conveyor systems or printing presses.
- Overload Protection: Automatically disengages when torque exceeds a set threshold, safeguarding machinery from damage.
- Maintenance-Free Operation: No brushes or friction surfaces to replace, reducing downtime.
Industry Applications:
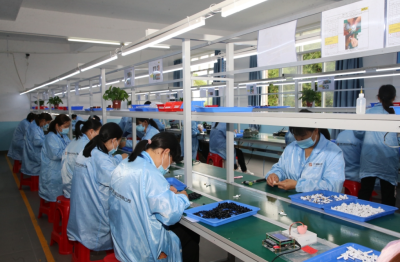
- Textile Manufacturing: Regulating thread tension in spinning machines.
- Robotics: Ensuring precise motion control in collaborative robots.
- Energy Storage: Managing torque in flywheel energy storage systems.
MOTOR TEST EQUIPMENT: THE BACKBONE OF QUALITY ASSURANCE
In an era where electric motors power everything from household appliances to electric vehicles, robust motor test systems are non-negotiable. These systems integrate hysteresis dynamometers, sensors, and software to deliver comprehensive performance validation.
Core Components of a Modern Motor Test System:
1. Dynamometer Integration: Hysteresis dynamometers provide the load necessary to simulate real-world operating conditions.
2. Data Acquisition: High-precision sensors capture torque, speed, temperature, and vibration data in real time.
3. Control Software: Customizable platforms allow engineers to design test cycles, analyze results, and generate compliance reports.
Benefits of Advanced Motor Testing:
- Reduced Time-to-Market: Automated testing protocols accelerate validation processes.
- Cost Savings: Early detection of design flaws minimizes post-production recalls.
- Regulatory Compliance: Ensures adherence to international standards like ISO, IEC, or SAE.
Case Study: Revolutionizing EV Motor Testing
A leading electric vehicle manufacturer recently adopted a hysteresis-based motor test system to evaluate the endurance of their next-generation drivetrain. By replicating extreme acceleration, regenerative braking, and thermal cycles, the system identified potential failure points months ahead of schedule, saving millions in potential warranty claims.
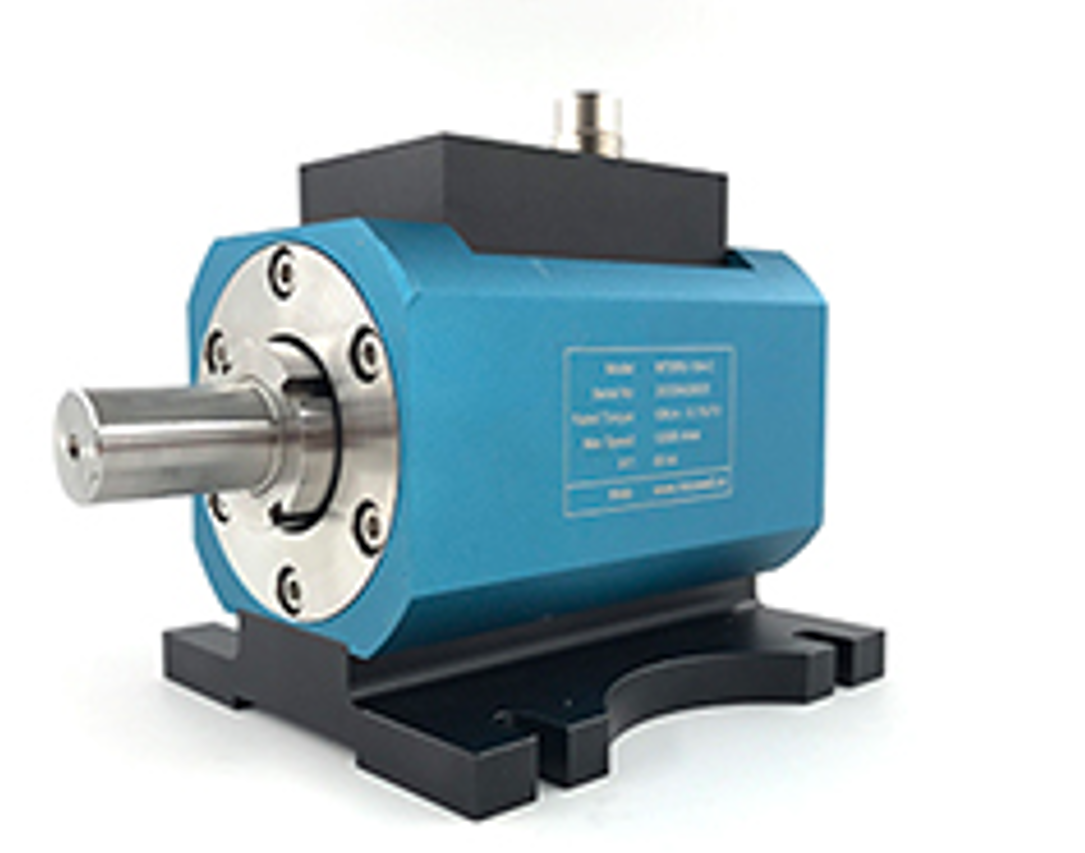
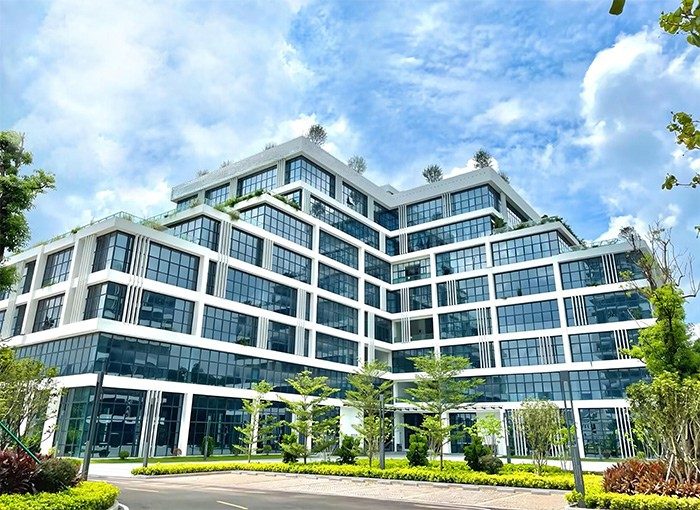
BUILDING A FUTURE-PROOF MOTOR TEST SYSTEM
To stay competitive, companies must adopt motor test systems that are scalable, adaptable, and capable of handling emerging technologies. Here’s how hysteresis-based solutions pave the way:
1. Adaptability to New Technologies:
As industries transition to hybrid and fully electric systems, test equipment must accommodate higher voltages, advanced materials, and IoT connectivity. Hysteresis systems, with their inherent flexibility, are well-suited to evolve alongside these trends.
2. Integration with Industry 4.0:
Modern motor test systems now feature:
- Cloud-Based Analytics: Remote monitoring and predictive maintenance capabilities.
- AI-Driven Optimization: Machine learning algorithms that identify efficiency improvements.
- Digital Twins: Virtual replicas of physical systems for risk-free scenario testing.
3. Sustainability Alignment:
By eliminating the need for hydraulic fluids or consumable friction components, hysteresis-based systems reduce environmental impact while lowering operational costs.
NAVIGATING THE SELECTION PROCESS: WHAT TO LOOK FOR
Choosing the right hysteresis brake, dynamometer, or test system requires careful consideration of several factors:
- Torque and Speed Requirements: Match the device’s capacity to your application’s peak demands.
- Control Precision: Ensure the system offers the resolution needed for your quality standards.
- Compatibility: Verify integration with existing software, sensors, or automation frameworks.
- Supplier Expertise: Partner with vendors who provide end-to-end support, from installation to training.
CONCLUSION: EMPOWERING INNOVATION THROUGH PRECISION
The convergence of hysteresis technology and advanced motor testing solutions represents a leap forward in industrial capability. From ensuring the reliability of life-saving medical devices to pushing the boundaries of electric mobility, these tools empower engineers to innovate with confidence.
As High-speed motor test systems continue to demand higher efficiency, quieter operation, and smarter systems, the role of hysteresis brakes, dynamometers, and integrated test platforms will only grow more vital. By investing in these technologies today, businesses position themselves at the forefront of tomorrow’s engineering challenges, ready to deliver solutions that are as precise as they are powerful.
Whether you’re designing the next breakthrough in clean energy or refining the motors that power everyday life, the right testing and control equipment isn’t just an asset—it’s a catalyst for progress. Embrace the precision of hysteresis technology, and unlock the full potential of your mechanical systems.